River300 | 28-33 Metric Ton Amphibious Excavator
This amphibious excavator, engineered for 28-33 tonnes of excavation, excels in demanding environments. Featuring our exclusive patented technology, it minimizes downtime and enhances productivity, effectively reducing operational costs. We also provide OEM services tailored to your specific needs.
Features of 28-33 Ton Amphibious Excavtors
- Large Pontoons RC300: Engineered for exceptional flotation, the RC300 pontoons provide 28.8 tons of buoyancy, enhancing stability in aquatic environments.
- Wider Overall Structure (5000mm): The 5000mm-wide structure offers increased stability and operator safety by distributing weight more evenly, reducing tipping risks.
- Three Separate Watertight Compartments per Pontoon: Each pontoon has three watertight compartments, improving safety and preventing sinking if one is damaged.
- Triple Chain Track System: This system efficiently distributes track pressure, reducing wear and extending the undercarriage’s life, especially in tough terrains.
- RD300 Positioning Pile Installation: With a total buoyancy of 32 tons when fully equipped, this installation boosts stability and operational capability.
- High-Strength Steel Construction: Constructed from corrosion-resistant and wear-resistant high-strength steel for durability and long service life.
- Fully Automatic Hydraulic Control System: Provides precise, efficient operation from the cab, enhancing overall productivity.
- Custom 13 to 18-Meter Long Reach Boom: Extends from 13 to 18 meters, ideal for applications requiring extended reach.
Specifications of 28-33 Ton Amphibious Excavators
River300 | Parameter | Unit |
Operating weight | 40380 | Kg |
Boom and stick length | 15000 | mm |
Bucket capacity | 0.6 | m³ |
Engine model | Cat C7.1 | / |
Rated power/speed | 225/2000 | Kw/rpm |
Max torque/speed | / | Nm/rpm |
Displacement | 7.01 | L |
Motor model | TM40 | Mottrol(Doosan) |
Output torque | 4651 | N.m(kgf.m) |
Continuous pressure | 350 | MPa(kgf/cm2) |
Driving speed | 4/2(max/min) | km/h |
Swing speed | 11.5 | r/min |
Gradeability | 《30° | ° |
Ground specific pressure | 25.6 | kPa |
Bucket digging force | 159 | kN |
Stick digging force | 106 | kN |
Fuel tank volume | 474 | L |
Hydraulic oil tank volume | 147 | L |
Engine oil capacity | 25 | L |
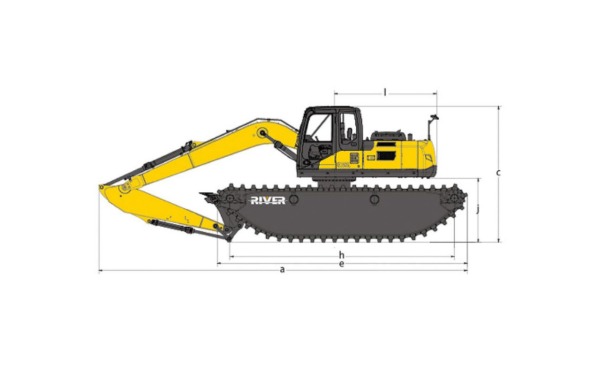
River300 | Parameter | Unit |
a) Overall machine length | 14500 | mm |
c) Overall machine height(to boom) | 4150 | mm |
e) Single pontoon length | 9000 | mm |
h) Distance between sprocket and idler | 8120 | mm |
j) Counterweight ground clearance | 2320 | mm |
l) Max turning radius of the tail | 3130 | mm |
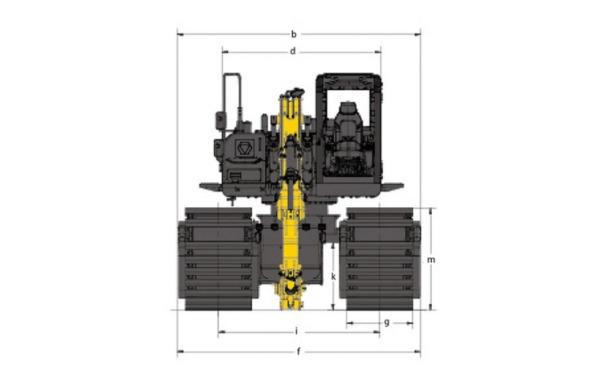
River300 | Parameter | Unit |
b) Overall machine width without side pontoons | 4800 | mm |
d) Turntable width | 3390 | mm |
f) Pontoon overall width | 4800 | mm |
g) Track shoe width | 1350 | mm |
i) Track gauge | 3200 | mm |
k) Min ground clearance | 1400 | mm |
m) Single pontoon height | 1900 | mm |
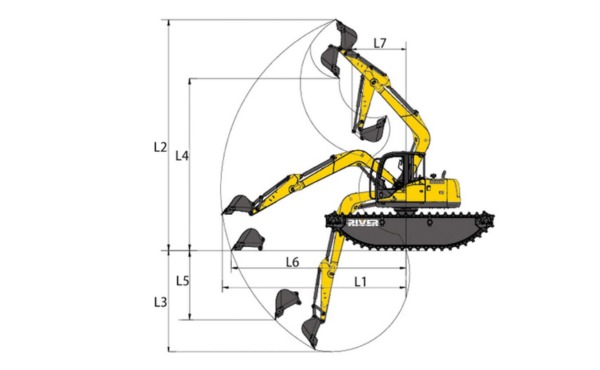
River300 | Parameter | Unit |
L1) Max digging radius | 16560 | mm |
L2) Max digging height | 16860 | mm |
L3) Max digging depth | 10750 | mm |
L4) Max unloading height | 14400 | mm |
L7) Min turning radius | 6750 | mm |
- The above specification is based on CAT330 excavator model with 15m long reach front, actual working range may vary from different excavator models.
Benefits of RIVER’s Amphibious Excavators
Our Lightweight Design was developed by our construction team’s over 15 years of experience in water projects, which means the pontoon buoyancy is less than the total machine weight (the upper structure and undercarriage of the excavator). By doing so, the amphibious excavator can work in shallow water and gain better flexibility under 1.8 meters (depending on the model).
- The excavator can land and manoeuvre stably in shallow water. All digging operations in different directions are as safe as land crawlers working on the ground without risk of rolling over;
- With a Lightweight Designed pontoon, customers enjoy a more compact appearance, easier marsh travel, and more flexible operation while saving on investment costs.
- A systematic series of side pontoons and spuds provided for pairing with different undercarriage models would allow the amphibious excavator to fully float in deeper water ranging from 1.6 meters to a maximum of 5 meters, which enables swamp buggy working in diversified work scenarios.
∗ Specialized Track Shoes Material
As the most essential wear part, the track shoe cleats we produce are of China WISCO’s super high strength welding structura steel HG785D whose yield strength is 685MPa and tensile strength is 785MPa. Its impact energy under -20℃ is above 47J, and it enjoys good weldability and formability. The same material is selected for reinforcing the conjunction part of the pontoon’s side plate and top plate which is one of the key parts deciding the framework’s firmness. We choose stronger material than any other competitors around the world to effectively avoid the pontoon structure from deformation, and wins exceedingly high comments from customers about our track shoe cleats’ wearability and durability.
∗ Track Chain Roller
We choose 40Cr steel (DIN 41Cr4) for our track chain rollers which are one of the important wear parts during excavator’s daily operation. All rollers must go through heat treatment including quenching and tempering to enhance the hardness to HRC50-56.
∗ Wear Pad for Resistance
We choose special wear-resistant material NM400 for the wear pad to ensure it would not be easily worn out by the track chains. High-class material selection of the wear pad will extend the pontoon’s lifetime by 1-2 years on average.
∗ Screws Adopted for Amphibious Excavator
All screws equipped on our swamp buggy are treated with Dacromet process, and must go through salt spray test which lasts for 1000 hours. This highly improves the anti-corrosion ability of the screws, and thus allows the excavator to work longer in more severe working environment. The maintenance and replacement cycle of spare parts are thus extended.
∗ Hydraulic Oil Pipes & Fittings
Both the hydraulic oil pipes and fittings are of imported famous brands with good durability. And the external surface of all oil pipes are wrapped with a protective PVC layer to enhance its anti-corrosion and wear-resistant ability. All oil pipes are arranged in good oder with tidy layout.
∗ Guide&Drive Wheel Heat Treatment
The front idler and the drive sprocket both go through special heat treatment to ensure reliable hardness and strength.
∗ Steel Plate Shearing & Bending
All the plate bending is done by China’s top brand NC press brake machine which ensures high accuracy and unified bending curves. While thick steel plates are cut by plasma cutting machine, thin plate cutting is done by laser cutting machine, both quick and accurate with the cutting edge in good order without any iron scurf.
∗ Robot Welding of Pontoon Undercarriage
All the buckets and part of our pontoon undercarriage are automatically welded by the robot arm, especially spot welding areas. This not only ensures high welding accuracy, but also helps improve the entire productivity as well as reduce resource consumption and possible environment pollution.
∗ H-frame Machining
We customize every H-frame in accordance to the slewing bearing dimensions of different excavator brands and models. Each H frame is machined as a whole by a gantry type machining center and the circle of bolting holes are milled by the hole milling machine. This secures accurate matching for complete assembly and also enhances the overall parts consistency of the amphibious excavator, which will provide better operation feedback for the operators.
∗ Compartment Gastight Test
After welding, all the three vacuum chambers of the pontoon must receive gastight testing where 4 standard atmospheric pressure will be charged and held for 15 minutes. Only ensured no leakage by the test as well as proved qualified by other examinations will our amphibious excavators be allowed to leave the factory.
∗ Amphibious Undercarriage Painting
A fully automatic shot-blasting and painting line which cost USD12.5 million is running for our pontoon’s surface treatment from rust removing, shot-blasting, polishing, puttying, priming to top finishing, and the coating surface is even and smooth. The paint we use is specialized type for marine ship coating which is hard, wearable with good gloss and not easy to peel off. Each pontoon must go through shot blasting till Sa2.5 grade with surface roughness within 30-70um before getting coated. The thickness of coating layer must achieve 160~200um and each pontoon must have 2 layers of primer and two layers of top coats.
∗ Professional Swamp Buggy Assembly/Disassembly Workshop
We have a professional and skilled crawler excavator workforce team for disassembling the chassis and assemblying our pontoon undercarriage with the upper body. With their strict technical standards for drive motor positioning, hydraulic oil pipeline installation, and bolt/screw tightening, etc, our marsh buggy‘s installation precision is highly assured. Every set of RIVER’s excavator will also have a travel test and conventional commissioning before delivered to our customer.
Applications of 28-33 Ton Amphibious Excavators
Why Choose River?
Since 2003, RIVER has excelled in the field of amphibious excavators and river dredging solutions. With over 200 projects and state-of-the-art facilities in Hubei and Jiangsu, our expertise and innovation are unparalleled. We are committed to quality and customer satisfaction, earning global recognition for our reliable and high-performance equipment. By choosing RIVER, you partner with a leader in the industry dedicated to excellence and long-term development. We invite you to visit our factory to see firsthand the superior craftsmanship and advanced technology we offer. Contact us to explore partnership opportunities and experience why RIVER is the preferred choice for your needs.
Related Amphibious Excavators
Ready to Elevate Your Excavation Projects?
Unlock the power of our 28-33 ton amphibious excavators and take your projects to the next level. Choose from customized OEM solutions perfectly tailored to your needs or flexible rental options for short-term projects.
Don’t wait! Contact us today to learn more about our amphibious excavators, their powerful attachments, OEM services, and rental opportunities.